废气治理破裂后修复的注意事项
在工业生产与环保***域,废气治理系统起着至关重要的作用。然而,由于各种原因,废气治理设备或管道可能会出现破裂情况。当这种情况发生后,及时且正确地进行修复是保障废气处理效果、维持生产正常运转以及符合环保要求的关键。以下是废气治理破裂后修复时需要注意的多个方面:
一、安全事项
(一)人员安全防护
1. 呼吸防护:废气治理系统破裂可能导致有害气体泄漏,维修人员必须佩戴合适的呼吸防护装备,如防毒面具或空气呼吸器。根据废气的成分和浓度,选择相应防护等级的面罩,确保能有效过滤或隔***有毒有害物质,防止维修人员吸入中毒或受到刺激性气体的伤害。
2. 身体防护:穿着防护服、防护手套和防护鞋等。防护服应具有防化性能,能够抵御废气中可能含有的腐蚀性、毒性物质对皮肤的侵害。防护手套要选择耐化学腐蚀的材质,如丁腈橡胶手套等,避免手部直接接触有害物质而受损。防护鞋则需具备防滑、防砸和防渗透功能,保障脚部安全。
3. 眼部防护:佩戴护目镜或面罩,防止飞溅的废气成分或因操作产生的碎片进入眼睛,造成眼部灼伤或其他伤害。
(二)环境安全评估
1. 气体检测:在进入修复现场前,必须使用专业的气体检测仪器对周边环境进行检测,确定空气中有害气体的浓度。检测的气体应包括但不限于废气中的主要成分、可能存在的易燃易爆气体以及氧气含量。如果有害气体浓度超标,需要先采取通风等措施降低浓度至安全范围,例如使用强力通风机进行空气置换,确保维修区域的空气符合安全标准,防止发生爆炸、中毒等事故。
2. 火灾与爆炸风险排查:对于一些含有易燃易爆成分的废气治理系统,破裂后可能形成可燃气体积聚的环境。要检查现场是否存在火源或潜在的点火源,如电气火花、静电、明火等,并采取相应的防火防爆措施。例如,关闭附近的非防爆电气设备,使用防爆工具进行操作,避免因摩擦、撞击产生火花引发爆炸事故。
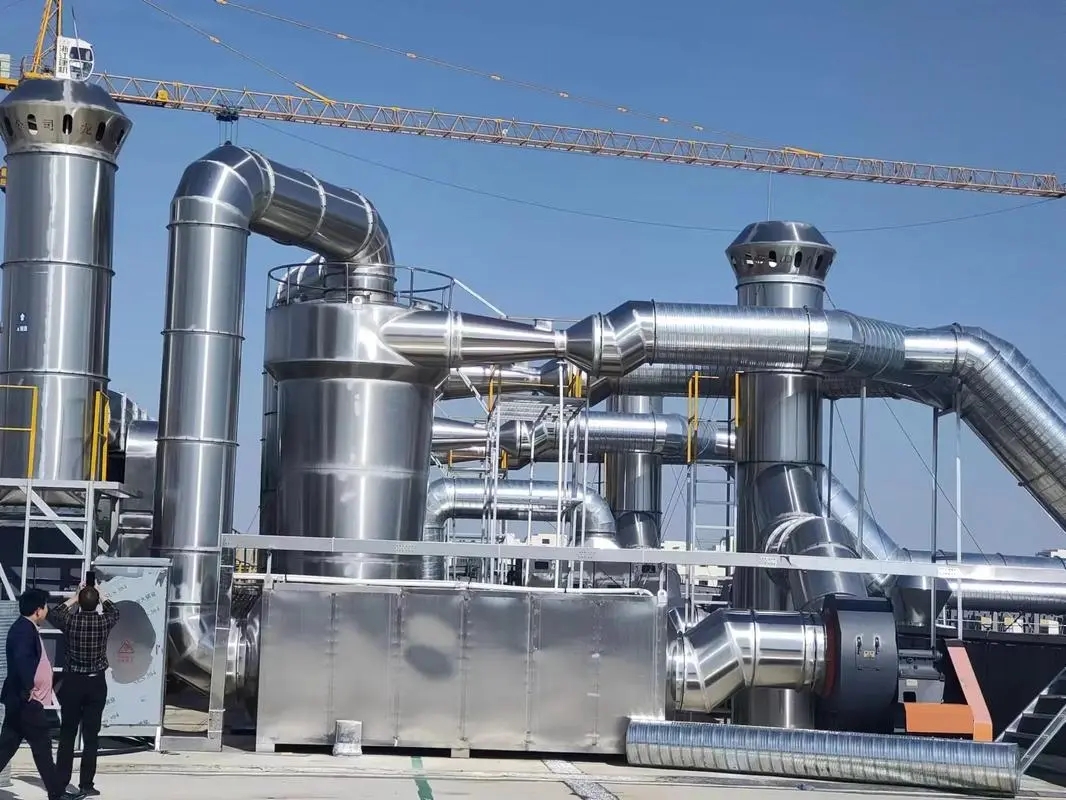
二、修复前的准备工作
(一)确定破裂原因与程度
1. 原因分析:仔细检查破裂部位,分析导致破裂的原因。可能是由于长期的化学腐蚀,使设备或管道的壁厚变薄;或者是物理应力作用,如压力波动、机械振动等造成的疲劳损坏;也有可能是外部因素,如自然灾害、人为碰撞等。准确判断破裂原因有助于采取针对性的修复措施,防止类似问题再次发生。
2. 程度评估:评估破裂的严重程度,包括破裂口的***小、形状、深度以及是否对周边结构造成影响。通过外观检查、无损检测(如超声波检测、射线检测等)等手段,确定破裂范围,判断是否需要对整个部件进行更换,还是可以通过局部修复解决问题。
(二)准备修复材料与工具
1. 材料选择:根据废气治理系统的材质、废气成分以及破裂情况选择合适的修复材料。如果系统是金属材质,对于较小的裂缝可以采用金属修补剂或焊接材料进行修复;对于较***的破损,可能需要使用金属补丁或更换部分管段。若是非金属材质(如玻璃钢、塑料等),则要选用对应的专用胶水、纤维布等材料进行修补。同时,要考虑材料的耐腐蚀性、耐高温性和强度等性能,确保修复后的部位能够长期稳定运行。
2. 工具配备:准备齐全修复所需的工具,如焊接设备(如果是焊接修复)、切割工具、打磨工具、扳手、螺丝刀等。对于一些***殊的修复方法,可能还需要专业的工具,如用于安装螺栓的扭矩扳手、用于粘接的专用夹具等。确保工具完***且能够正常使用,以提高修复效率和质量。
三、修复过程中的要点
(一)表面处理
1. 清洁:对破裂部位及其周边区域进行彻底清洁,去除油污、灰尘、铁锈等杂质。可以使用清洗剂、砂纸、钢丝刷等工具进行清洁,确保表面干净、干燥,以保证修复材料与原表面能够******粘结或焊接。
2. 打磨:对破裂口边缘进行打磨处理,使其形成一定的坡口,增加修复材料的接触面积和结合力。打磨时要控制***角度和粗糙度,避免过度打磨导致部件厚度减小过多,影响其强度。对于金属表面,一般要求打磨至露出金属光泽;对于非金属表面,则要根据材料***性和修复要求进行适当打磨。
(二)修复操作
1. 焊接修复:如果采用焊接方式修复金属部件,要严格按照焊接工艺规范进行操作。选择合适的焊接材料和焊接参数,如电流、电压、焊接速度等。在焊接过程中,要注意防止焊接变形,可以采用对称焊、分段焊等方法减少变形量。同时,要保证焊接质量,避免出现气孔、夹渣、未焊透等缺陷,焊接完成后进行焊缝检测,如外观检查、无损检测等,确保焊缝的密封性和强度。
2. 粘接修复:对于非金属或不适合焊接的部位,可以采用粘接方法修复。按照粘接剂的使用说明,将粘接剂均匀涂抹在破裂部位和修复材料表面,然后将修复材料贴合在破损处,施加适当的压力,使其紧密结合。在粘接过程中,要注意控制环境温度和湿度,保证粘接效果。固化期间要保持压力稳定,避免修复材料移位,待粘接剂完全固化后,才能进行后续操作。
3. 补丁修复:当破裂口较***时,可以使用补丁进行修复。制作合适形状和尺寸的补丁,材料要与原部件相匹配或具有更***的性能。将补丁安装在破裂部位,通过螺栓连接、焊接或粘接等方式固定牢固。在安装补丁时,要确保其与原部件表面紧密贴合,无缝隙,防止废气泄漏。
(三)密封处理
1. 密封材料选择:修复完成后,对修复部位进行密封处理,防止废气泄漏。根据废气的温度、压力、化学成分等条件选择合适的密封材料,如密封胶、垫片等。密封材料要具有******的耐化学腐蚀性、耐高温性和弹性,能够适应废气治理系统的工作环境。
2. 密封操作:在密封操作时,要确保密封材料填充均匀、充实,无气泡、裂缝等缺陷。对于法兰连接部位,要更换新的垫片,并拧紧螺栓,保证法兰之间的密封性。对于一些无法使用垫片的部位,可以使用密封胶进行密封,涂抹密封胶时要连续、均匀,覆盖整个需要密封的区域,确保修复后的系统具有******的密封性能。
四、修复后的检查与测试
(一)外观检查
1. 修复部位检查:对修复后的部位进行全面的外观检查,查看修复材料是否与原部件表面平整一致,有无凹陷、凸起、裂缝、孔洞等缺陷。对于焊接修复的部位,检查焊缝的余高、宽度是否符合要求,有无焊接缺陷;对于粘接或补丁修复的部位,检查是否有脱胶、松动现象。
2. 整体检查:除了修复部位,还要对整个废气治理系统进行外观检查,查看是否有因修复操作导致的其他部件损坏或变形,如管道的位移、支架的松动等。确保系统的整体外观完***,无异常情况。
(二)泄漏测试
1. 压力测试:对于一些能够承受压力的废气治理管道或设备,可以进行压力测试。使用压缩空气或惰性气体向系统内充压,使其达到工作压力或略高于工作压力的状态,然后使用肥皂水、喷雾器等工具对修复部位及周边连接处进行检漏。观察是否有气泡产生,如有气泡出现,说明存在泄漏点,需要重新进行修复和密封处理。
2. 真空测试:对于一些密封性要求较高的小型设备或部件,可以采用真空测试方法。将修复后的部件放入真空环境中,通过抽取空气使其内部形成一定的负压,然后观察是否有压力回升现象,如果有压力回升,说明存在泄漏,需要进行进一步检查和修复。
3. 气体浓度监测:在废气治理系统正常运行状态下,使用气体检测仪器对修复部位周边的气体浓度进行监测。如果发现有害气体浓度异常升高,说明可能存在微小泄漏点,需要仔细排查并进行处理。
(三)性能测试
1. 处理效果测试:在修复后的废气治理系统投入正常运行后,对其进行处理效果测试。采集系统进口和出口的废气样本,分析废气中污染物的浓度变化,如颗粒物浓度、有害气体浓度(如二氧化硫、氮氧化物、挥发性有机物等)等。确保修复后的系统能够达到设计要求的废气处理效率,保证排放的废气符合***家或地方的环保标准。
2. 运行参数监测:监测废气治理系统的运行参数,如风机的风量、风压,设备的运行温度、压力等。这些参数应保持在正常范围内,与修复前相比不应有明显异常变化。如果发现运行参数异常,可能意味着修复工作影响了系统的整体性能,需要进一步检查和调整。
五、后续维护与预防措施
(一)定期维护
1. 检查周期:建立定期检查制度,对修复后的废气治理系统进行定期检查。检查周期可以根据系统的使用频率、运行环境、废气成分等因素确定,一般建议每周或每月进行一次外观检查,每季度或半年进行一次全面的性能测试和泄漏测试。
2. 维护内容:定期检查内容包括修复部位的密封性、设备的运行状况、管道的连接情况等。对发现的小问题及时进行处理,如紧固松动的螺栓、更换老化的密封件等,避免问题扩***化。同时,对废气治理系统的其他部件也进行维护保养,如清洗过滤器、检查仪表精度等,确保整个系统处于******的运行状态。
(二)预防措施
1. 操作规范培训:加强对操作人员的培训,使其熟悉废气治理系统的操作规程和注意事项。操作人员应严格按照操作规范进行操作,避免因误操作导致设备或管道损坏。例如,控制废气的流量、温度、压力在合理范围内,避免剧烈的压力波动或温度变化对系统造成冲击。
2. 环境监控与保护:对废气治理系统周围的环境进行监控,如温度、湿度、腐蚀性气体浓度等。采取相应的环境保护措施,如安装空调、除湿设备,控制环境温度和湿度;对存在腐蚀性气体的环境,进行通风换气或采取防腐措施,减少环境因素对系统的腐蚀和损害。
3. 备用部件准备:储备一些常用的废气治理系统部件,如管道、阀门、过滤器等。一旦出现部件损坏的情况,能够及时更换,减少系统停机时间,保证生产的连续性和环保达标排放。
总之,废气治理破裂后的修复工作是一项复杂而细致的任务,需要从安全、修复前准备、修复过程、修复后检查到后续维护等多个环节入手,严格遵守相关注意事项,才能确保修复质量,使废气治理系统恢复正常运行,有效保护环境和人员健康。